*CONTROL_ADAPTIVE
Deep Drawing with Adaptivity
LS-DYNA Manual Section: *CONTROL_ADAPTIVE
Additional Sections:
*DAMPING_GLOBAL
*LOAD_RIGID_BODY
Example: Deep Drawing with Adaptivity
Filename: control_adaptive.cup-draw.k
Description:
This problem includes three tools a punch, a binder and a die and also includes
a blank to be formed. The blank is deep drawn by the punch while the binder
and die hold the blank edges and help prevent wrinkling. During the process,
adaptivity is employed to refine the mesh of the blank to improve accuracy.
Model:
Only 1/4 of the system is modeled because of symmetry. The binder pushes down
on the blank against the die using a * LOAD_RIGID command to model the boundary
edge condition. The punch is moved down onto the blank with a
*BOUNDARY_PRESCRIBED_MOTION_RIGID command. Global damping and contact damping
are defined to prevent local nodal vibrations. The time-step size is controlled
with mass scaling because inertial effects are insignificant in this problem.
One way surface to surface contact is defined between the major parts.
This allows the drawing (i.e., contact) forces to be monitored using the
rcforc ascii output file.
Results:
During the drawing operation, the mesh is refined considerably.
$ *BOUNDARY_PRESCRIBED_MOTION_RIGID
$ - the binder pushes down on the blank against the die using a *LOAD_RIGID
$ - there are a lot of constrained nodes defined in *NODE (tc,rc)
*BOUNDARY_PRESCRIBED_MOTION_RIGID
*CONTACT_ONE_WAY_SURFACE_TO_SURFACE
*CONTROL_ADAPTIVE
*CONTROL_CONTACT
*CONTROL_ENERGY
*CONTROL_OUTPUT
*CONTROL_SHELL
*CONTROL_TERMINATION
*CONTROL_TIMESTEP
*DAMPING_GLOBAL
*DATABASE_BINARY_D3PLOT
*DATABASE_GLSTAT
*DATABASE_MATSUM
*DATABASE_RBDOUT
*DATABASE_RCFORC
*DEFINE_CURVE
*ELEMENT_SHELL
*END
*KEYWORD
*LOAD_RIGID_BODY
*MAT_PLASTIC_KINEMATIC
*MAT_RIGID
*NODE
*PART
*SECTION_SHELL
*SET_PART
*TITLE
*KEYWORD
*TITLE
deep drawing - blankholder contact damping , mesh refinement
$
$ LSTC Example
$
$ Last Modified: October 14, 1997
$
$ - adaptive meshing
$
$ - the binder pushes down on the blank against the die using a *LOAD_RIGID
$ for the boundary edge condition
$
$ - the punch is moved down onto the blank with a
$ *BOUNDARY_PRESCRIBED_MOTION_RIGID
$
$ - global damping and contact damping
$
$ - time step is controlled with mass scaling
$
$ - there are a lot of constrained nodes defined in *NODE (tc,rc)
$
$
$ Units: gm, cm, micro-s, 1e7N, Mbar, 1e7N-cm
$
$$$$$$$$$$$$$$$$$$$$$$$$$$$$$$$$$$$$$$$$$$$$$$$$$$$$$$$$$$$$$$$$$$$$$$$$$$$$$$$$
$
$$$$ Control Ouput
$
$$$$$$$$$$$$$$$$$$$$$$$$$$$$$$$$$$$$$$$$$$$$$$$$$$$$$$$$$$$$$$$$$$$$$$$$$$$$$$$$
$
$...>....1....>....2....>....3....>....4....>....5....>....6....>....7....>....8
$
*CONTROL_TERMINATION
$ endtim endcyc dtmin endneg endmas
700.0
$
*CONTROL_CONTACT
$ slsfac rwpnal islchk shlthk penopt thkchg orien
.01 0. 2 1
$ usrstr usrfrc nsbcs interm xpene ssthk ecdt tiedprj
$
*CONTROL_ENERGY
$ hgen rwen slnten rylen
2 2 2
$
*CONTROL_OUTPUT
$ npopt neecho nrefup iaccop opifs ipnint ikedit
1 3
$
*CONTROL_SHELL
$ wrpang itrist irnxx istupd theory bwc miter
20.0 1 0 1
$
*CONTROL_TIMESTEP
$ dtinit scft isdo tslimt dtms lctm erode ms1st
0. 0. 0 0. -0.25 0 0
$
$
*DATABASE_BINARY_D3PLOT
$ dt lcdt
40.0
$
*DATABASE_GLSTAT
$ dt
1.0
$
*DATABASE_MATSUM
$ dt
1.0
$
*DATABASE_RBDOUT
$ dt
5.0
$
*DATABASE_RCFORC
$ dt
1.0
$
$$$$$$$$$$$$$$$$$$$$$$$$$$$$$$$$$$$$$$$$$$$$$$$$$$$$$$$$$$$$$$$$$$$$$$$$$$$$$$$$
$
$$$$ Adaptivity
$
$$$$$$$$$$$$$$$$$$$$$$$$$$$$$$$$$$$$$$$$$$$$$$$$$$$$$$$$$$$$$$$$$$$$$$$$$$$$$$$$
$
$...>....1....>....2....>....3....>....4....>....5....>....6....>....7....>....8
$
*CONTROL_ADAPTIVE
$ adpfreq adptol adpopt maxlvl tbirth tdeath lcadp ioflag
5.0e+0 0.1 2 2 0.0 0.0 0
$
$
*DAMPING_GLOBAL
$ lcid valdmp
3
$
*DEFINE_CURVE
$ lcid sidr scla sclo offa offo
3
$ abscissa ordinate
0.000E+00 0.000E+00
1.000E+04 0.000E+00
1.001E+04 3.000E+03
2.000E+04 3.000E+03
$
$$$$$$$$$$$$$$$$$$$$$$$$$$$$$$$$$$$$$$$$$$$$$$$$$$$$$$$$$$$$$$$$$$$$$$$$$$$$$$$$
$
$$$$ Loading and Boundary Conditions
$
$$$$$$$$$$$$$$$$$$$$$$$$$$$$$$$$$$$$$$$$$$$$$$$$$$$$$$$$$$$$$$$$$$$$$$$$$$$$$$$$
$
$...>....1....>....2....>....3....>....4....>....5....>....6....>....7....>....8
$
*BOUNDARY_PRESCRIBED_MOTION_RIGID
$ pid dof vad lcid sf vid death
1 2 0 1 -1.
$
*DEFINE_CURVE
$ lcid sidr scla sclo offa offo
1
$ abscissa ordinate
0.000E+00 0.000E+00
1.000E+02 2.912E-03
2.000E+02 5.540E-03
3.000E+02 7.625E-03
4.000E+02 8.963E-03
5.000E+02 9.425E-03
6.000E+02 8.963E-03
7.000E+02 7.625E-03
8.000E+02 5.540E-03
9.000E+02 2.912E-03
1.000E+03 0.000E+00
$
$ From a sheet metal forming example. A blank is hit by a punch, a binder is
$ used to hold the blank on its sides. The rigid holder (part 2) is held
$ against the blank using a load applied to the cg of the holder.
$
$ The direction of the load is in the y-direction (dof=2) but is scaled
$ by sf = -1 so that the load is in the correct direction. The load
$ is defined by load curve 2.
$
$
*LOAD_RIGID_BODY
$...>....1....>....2....>....3....>....4....>....5....>....6....>....7....>....8
$ pid dof lcid sf cid m1 m2 m3
2 2 2 -1.0
$
*DEFINE_CURVE
$ lcid sidr scla sclo offa offo
2
$ abscissa ordinate
0.000E+00 8.000E-05
1.000E+04 8.000E-05
$
$$$$$$$$$$$$$$$$$$$$$$$$$$$$$$$$$$$$$$$$$$$$$$$$$$$$$$$$$$$$$$$$$$$$$$$$$$$$$$$$
$
$$$$ Define Parts and Materials
$
$$$$$$$$$$$$$$$$$$$$$$$$$$$$$$$$$$$$$$$$$$$$$$$$$$$$$$$$$$$$$$$$$$$$$$$$$$$$$$$$
$
$...>....1....>....2....>....3....>....4....>....5....>....6....>....7....>....8
$
*PART
$ pid sid mid eosid hgid grav adpopt
punch
1 1 2 0 0 0 0
binder
2 1 2 0 0 0 0
blank
3 1 1 0 0 0 1
die
4 1 2 0 0 0 0
$
$
*MAT_PLASTIC_KINEMATIC
$ mid ro e pr sigy etan beta
1 2.700E+00 0.690E+00 3.000E-01 8.180E-04 0.010E+00 1.000E+00 0.000E+00
$ src srp fs
0.000E+00 0.000E+00
$
$
*MAT_RIGID
$ mid ro e pr n couple m alias
2 8.450E-00 0.690E+00 3.000E-01 0.000E+00 0.000E+00 0.000E+00 0.000E+00
$ cmo con1 con2
0.000E+00 0.000E+00
$ lco/a1 a2 a3 v1 v2 v3
$
$
*SECTION_SHELL
$ sid elform shrf nip propt qr/irid icomp
1 2 1. 5. 0. 0. 0
$ t1 t2 t3 t4 nloc
.100 .100 .100 .100
$
$$$$$$$$$$$$$$$$$$$$$$$$$$$$$$$$$$$$$$$$$$$$$$$$$$$$$$$$$$$$$$$$$$$$$$$$$$$$$$$$
$
$$$$ Define Contacts - sliding interface definitions
$
$$$$$$$$$$$$$$$$$$$$$$$$$$$$$$$$$$$$$$$$$$$$$$$$$$$$$$$$$$$$$$$$$$$$$$$$$$$$$$$$
$
$...>....1....>....2....>....3....>....4....>....5....>....6....>....7....>....8
$
$$$$$ contact between blank (slaves) and punch (master)
$
*CONTACT_ONE_WAY_SURFACE_TO_SURFACE
$ ssid msid sstyp mstyp sboxid mboxid spr mpr
3 1 2 2 0 0 0 0
$
$ fs fd dc vc vdc penchk bt dt
.2 .2 0 0 20. 0 0 0
$
$ sfs sfm sst mst sfst sfmt fsf vsf
0 0 0 0 0 0 0 0
$
$
$$$$$ contact between blank (slaves) and binder (master)
$
*CONTACT_ONE_WAY_SURFACE_TO_SURFACE
3 2 2 2 0 0 0 0
.2 .2 0 0 20. 0 0 0
0 0 0 0 0 0 0 0
$
$
$$$$$ contact between blank (slaves) and die (master)
$
*CONTACT_ONE_WAY_SURFACE_TO_SURFACE
3 4 2 2 0 0 0 0
.2 .2 0 0 20. 0 0 0
0 0 0 0 0 0 0 0
$
$
*SET_PART
$ sid
3
$ pid
3
$
*SET_PART
1
1
$
*SET_PART
2
2
$
*SET_PART
4
4
$
$$$$$$$$$$$$$$$$$$$$$$$$$$$$$$$$$$$$$$$$$$$$$$$$$$$$$$$$$$$$$$$$$$$$$$$$$$$$$$$$
$
$$$$ Define Nodes and Elements
$
$$$$$$$$$$$$$$$$$$$$$$$$$$$$$$$$$$$$$$$$$$$$$$$$$$$$$$$$$$$$$$$$$$$$$$$$$$$$$$$$
$
$...>....1....>....2....>....3....>....4....>....5....>....6....>....7....>....8
$
$
*END
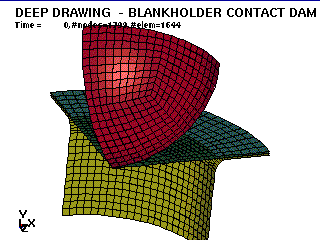