DUAL-CESE
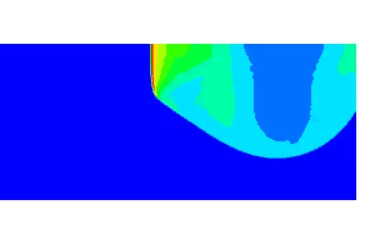
Slab of explosive in a stick form
In this test case, a slab of explosive in a stick form is confined by an inert material before detonating. This example tests one of the multiphase flow solvers with hybrid formulation and makes use of a JWL equation of state .
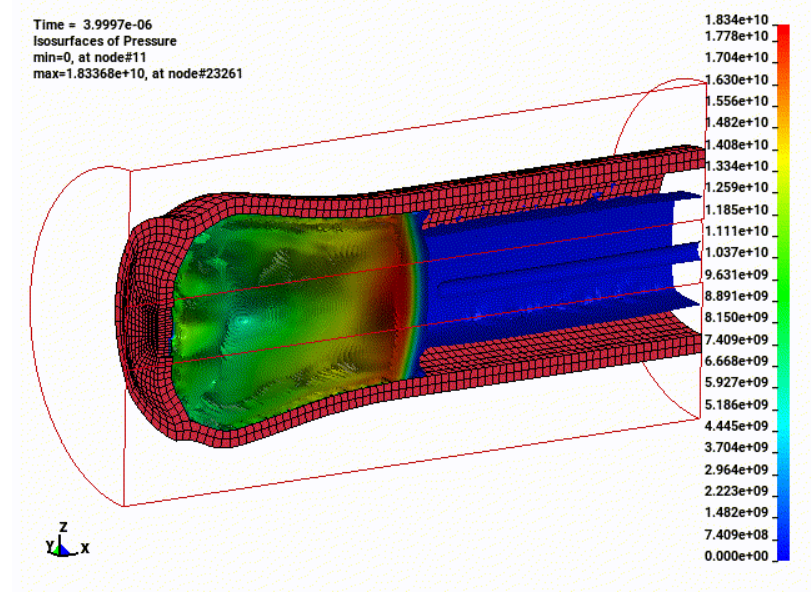
Slab of explosive confined in 3D cylinder
In this test case, a slab of explosive in a stick form, is confined inside a container. The explosive material is initiated by the booster, which forms a detonation wave that propagates to the right in reactive material (explosives). The high pressure behind the detonation front forces the structure confiner to deformation. The explosive considered in this scenario is LX-17 and the Ignition and Growth (I&G) reaction rate law is assumed.
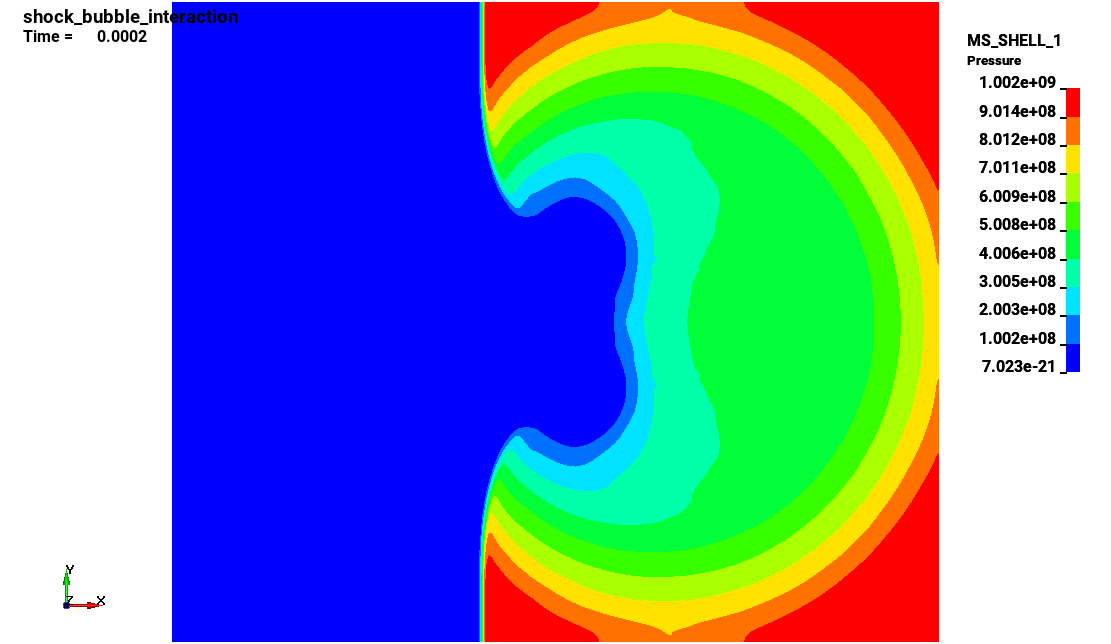
Shock Bubble interaction
In this 2D problem, a left moving shock wave propagates first through the stiffened gas before it hits a stationary bubble, which gains speed and loss its circular shape. After the shock wave hits the bubble, circular pressure waves are created, while a pair of vortices appears on the tail of the bubble, increasing the pattern complexity of the interface. This example is a classic multiphase flow example and is used to test our two-phase multiphase flow solver.
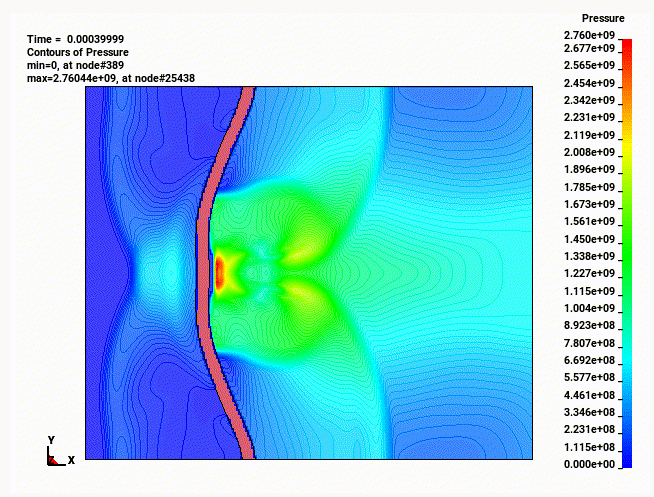
Shock Bubble interaction (+FSI) (+3D)
This FSI case is an expansion of the two-phase shock bubble example and adds a flexible structure (baffle) to the problem. In this test case, a left moving shock wave propagates and first hits a stationary bubble, which gains speed and loses its circular shape. After the shock wave hits the bubble, the created circular pressure waves keep moving forward and hit the structure panel causing its deformation. A 2D version and a 3D version of the problem are provided.
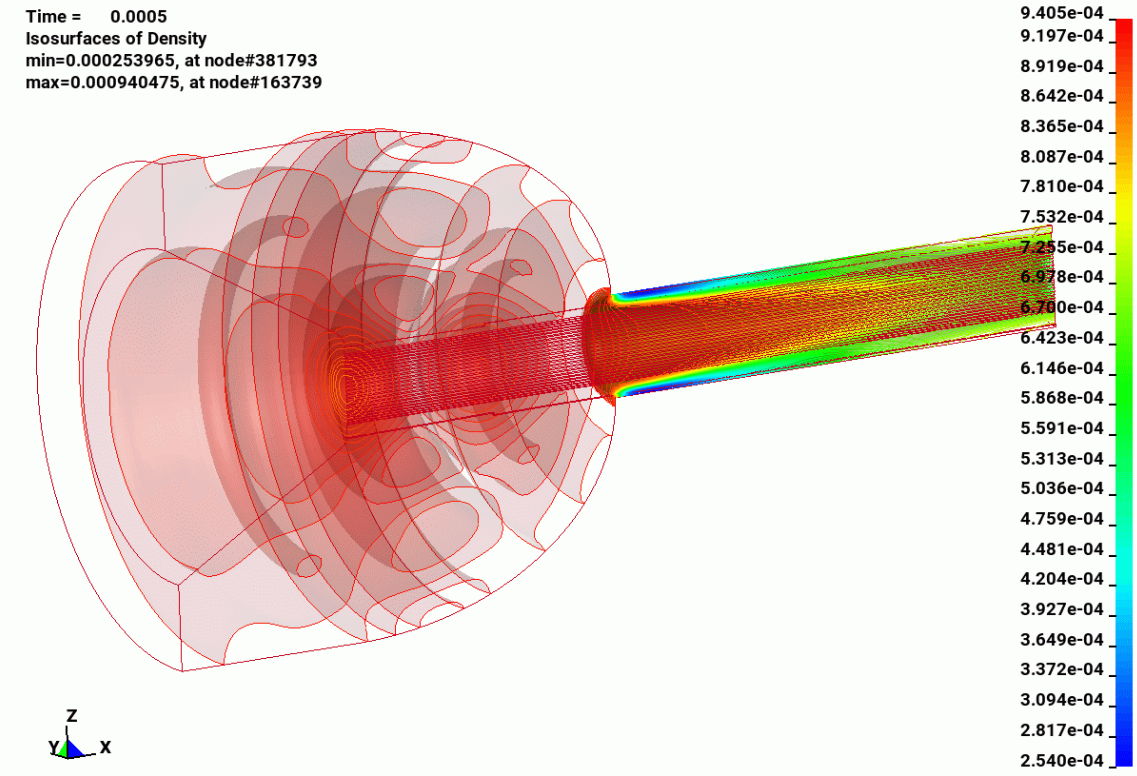
Cavitation in nozzle
This model gives an example of a cavity model implemented in the dual CESE solver. The cavitation model used is the Schmidt’s homogeneous equilibrium model (HEM), which is based on the acoustic speed of the mixture of liquid and vapor. This model is simple but contains the important characteristic information of cavitating flows. This cavitation model is very suitable for high-speed flows in small geometry, like diesel injection systems. both a 2D model and a 3D model are provided.
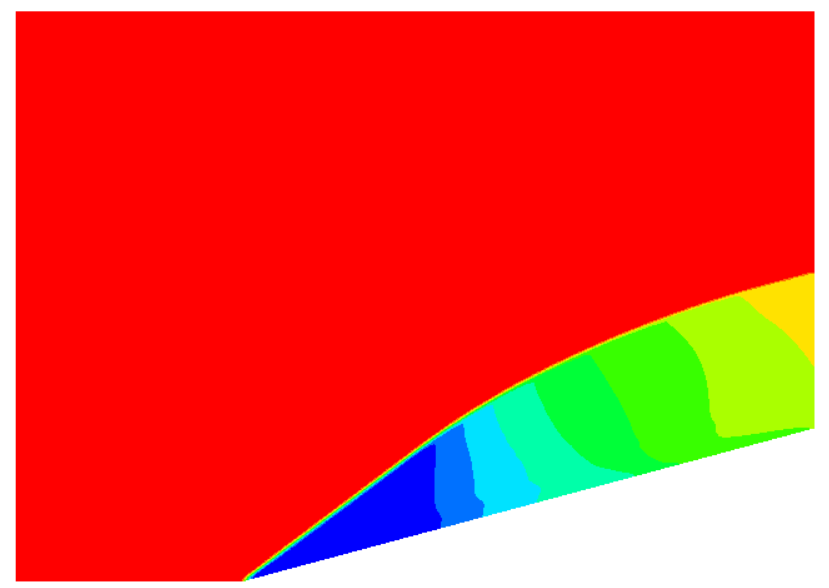
Supersonic Flow over 15° Ramp
This is a well known verification model for shock wave capture. A supersonic flow over a 15° ramp is modeled, and because of the ramp, an oblique shock wave is formed. The Inlet Mach number is about 2.5, density is 1.22 kg/m3 and temperature is 289 K.
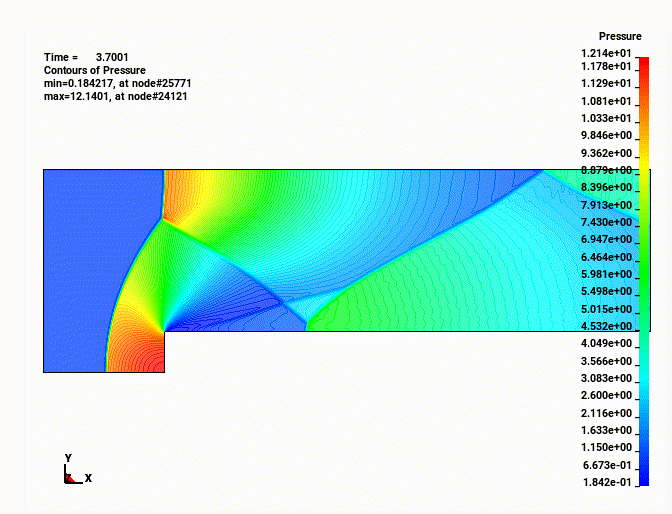
Forward Facing Step
This is a well known benchmarking problem for supersonic flow shock capturing. An incoming shock wave hits a forward facing step and reflects on the different walls, creating a transient shock wave pattern.
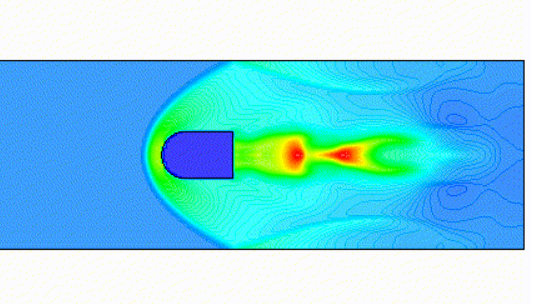
2D Projectile
In this test case, a fast-moving bullet in a shot tube after it is triggered is simulated with dual CESE FSI-IBM solver. The interface between the fluid and structure(bullet) will be detected automatically and handled
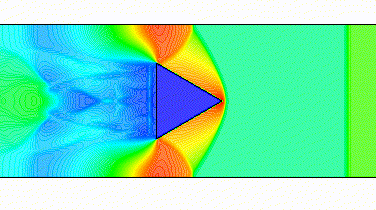
Moving Wedge Shock Wave Interaction
In this test case, a shock wave (initially located at the left boundary) is moving from left to right while a rigid body structural wedge is moving in the opposite direction. From the simulation results, we can see a complicated flow pattern because of the interactions between the off-body shock produced by the moving wedge, the upcoming shock, and the wedge.
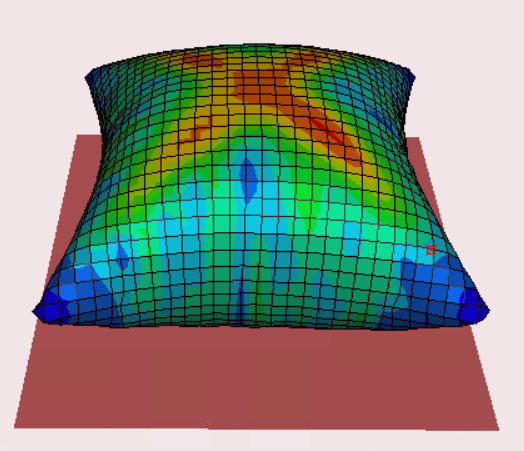
Folded bag deployment
This is a 3D fluid-structure interaction (FSI) problem solved with the dual CESE FSI solver using the immersed boundary method (ibm). In this test, a folded bag is deployed by a high-pressure jet from the entry tube.
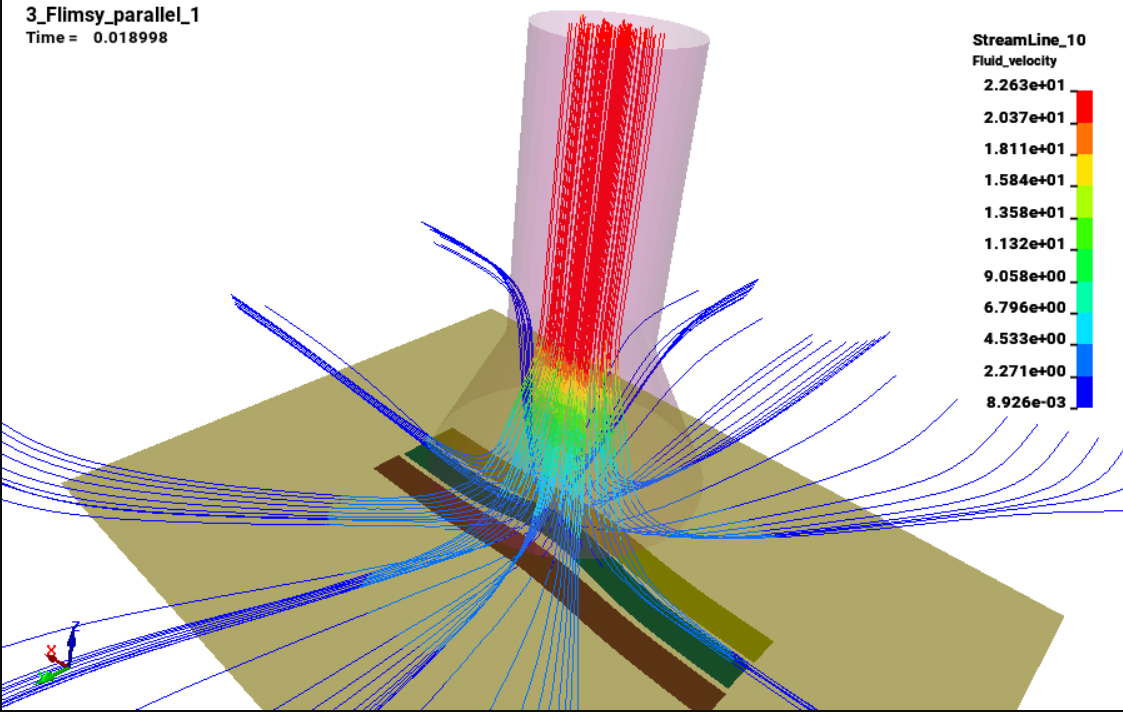
Vacuum Tube
In this FSI test case, three pieces of flimsy placed on a table are sucked by a vacuuming tube. The sucking process and the interaction between the flimsy and the fluid is simulated including the deformation pattern of the flimsy.
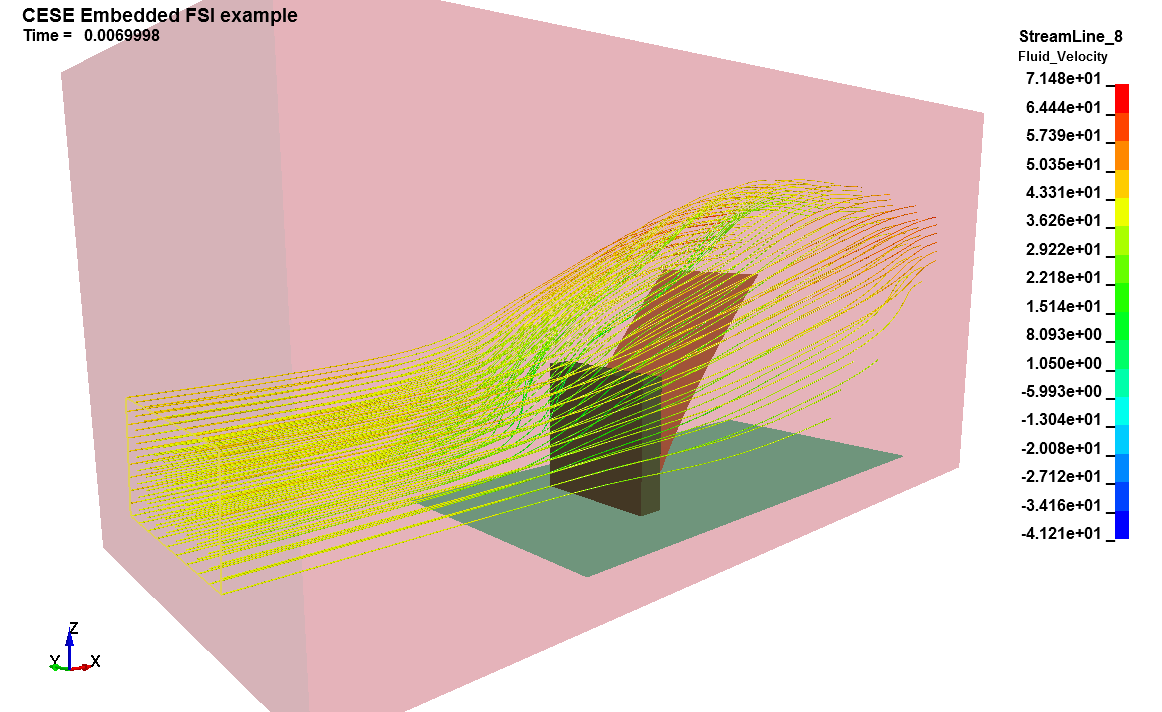
Embedded FSI example (DualCESE version)
This examples features a simple immersed FSI example. The active structure needs to be entirely embedded in the fluid for the immersed method. Interfaces are tracked automatically. It is advised to use a finer mesh for the fluid than for the solid. For FSI problems, the two solvers will use a synchronized timestep i.e the smallest value computed from their respective domains (CFL condition). No leakage can occur.
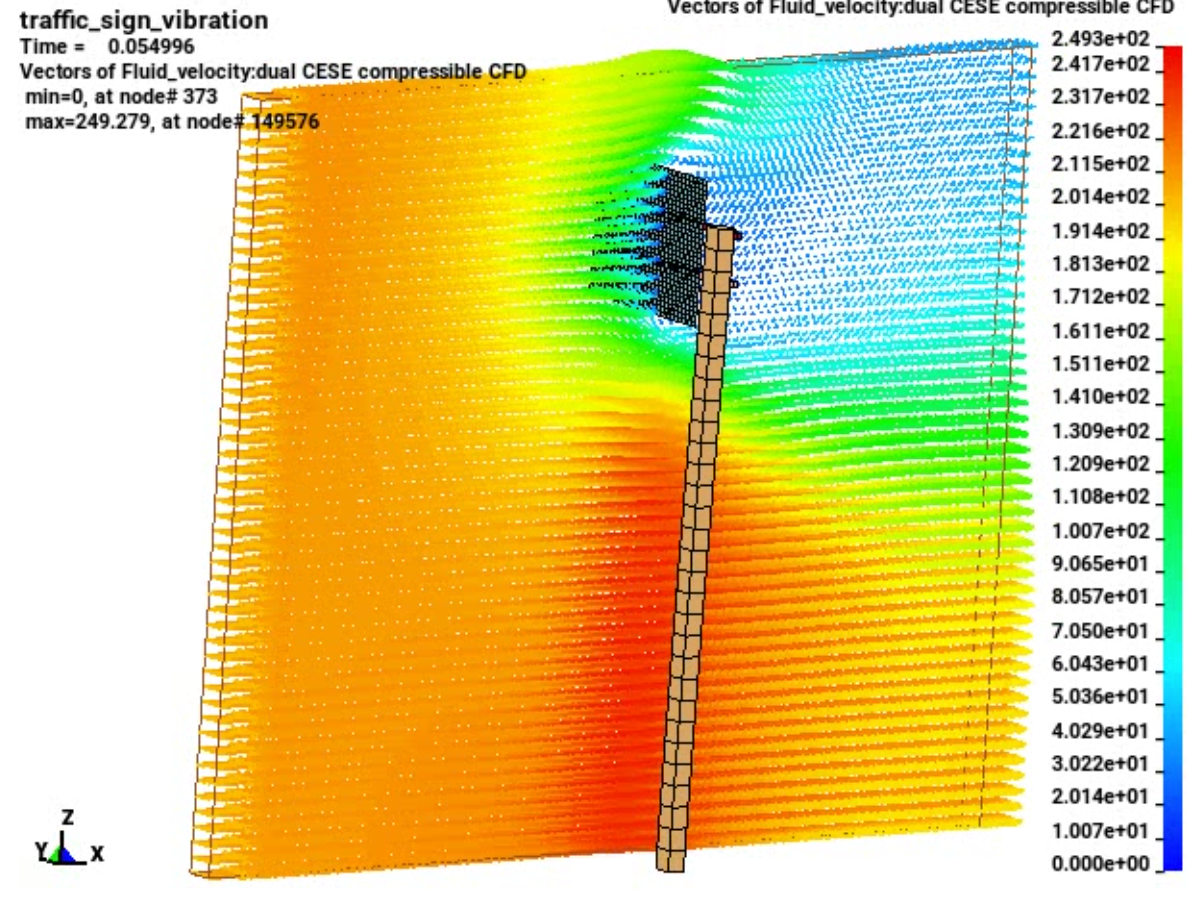
Traffic Sign Deflection
In this 3D FSI test case, the reaction of a traffic light plate due to a strong wind gust is simulated.
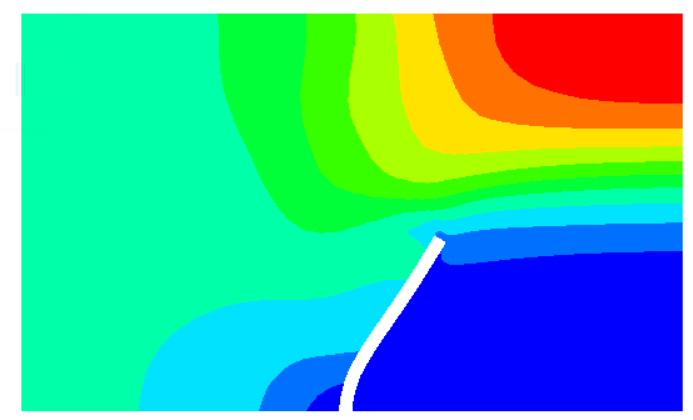
2D Pole Deformation
This is a 2D fluid-structure interaction (FSI) problem. In this test, a structure pole (shell element) stands in the middle of a flow field and its bottom end is fixed. When a strong wind flows from left to right, it pushes the pole and forces it to deform. It is simulated by the dual CESE FSI-mmm solver (this FSI solver is based on the moving mesh method (mmm), and can be more accurate than the immersed boundary method (ibm) in capturing small deformation problems).
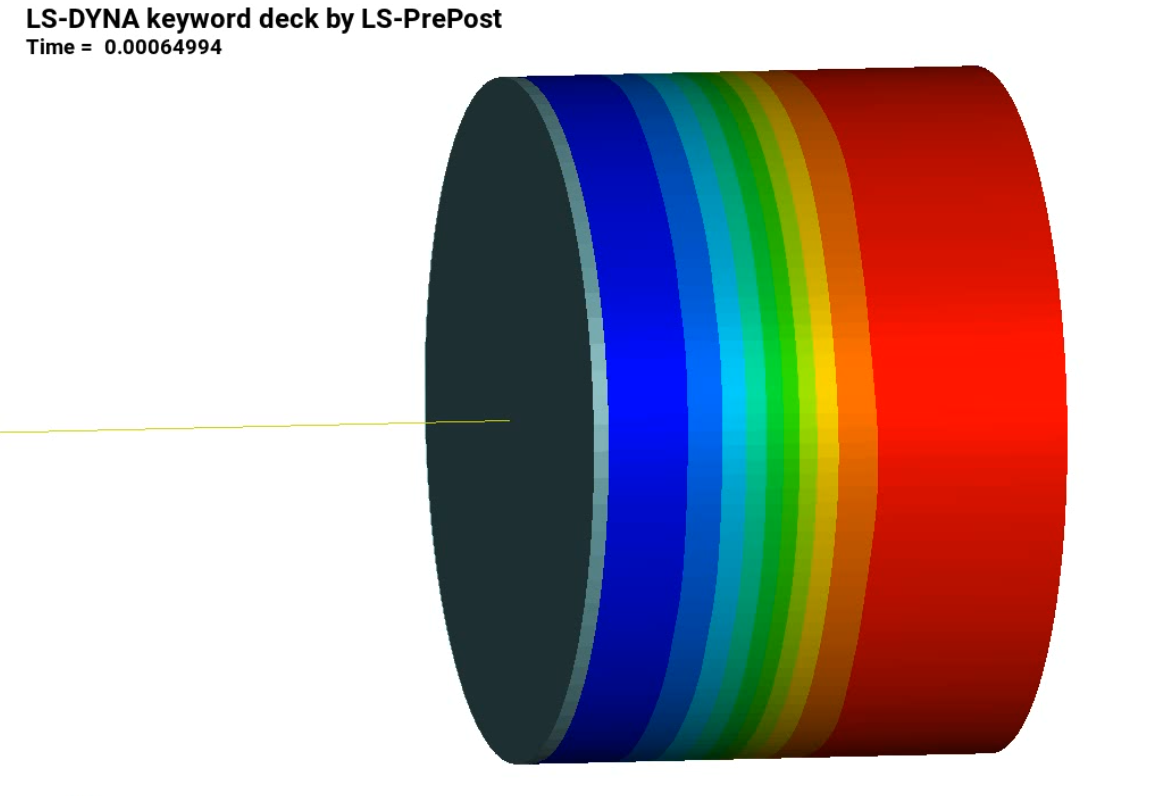
3D Piston Problem
In this 3D fluid-structure interaction (FSI) example, the flow field inside the piston chamber is simulated during the valve’s back and forth motion. Here the dual CESE FSI-mmm solver is used, which is based on the moving mesh method (mmm). This method is more suitable for small deformation problems.